In today’s competitive and technology-driven manufacturing landscape, the need for precision, quality, and efficiency has never been greater. Companies must meet increasingly stringent standards while optimizing resource use to remain competitive. Understanding Statistical Process Control (SPC) and data analytics are powerful methodologies for achieving these objectives, enabling organizations to manage production processes efficiently and minimize waste, defects, and downtime.
This article delves into SPC, the role of data analytics in enhancing SPC, and how organizations can leverage these tools to ensure high-quality outcomes in manufacturing and other process-driven industries.
Understanding Statistical Process Control (SPC)
Statistical Process Control (SPC) is a methodology that uses statistical methods to monitor and control a process. Developed in the early 20th century by Walter A. Shewhart, SPC has since evolved and expanded, now widely used across various industries, including manufacturing, automotive, aerospace, and pharmaceuticals. SPC aims to ensure that processes are stable, consistent, and capable of meeting desired specifications, reducing variability and identifying the sources of defects.
SPC primarily involves the following key components:
- Control Charts
Control charts are the core of SPC. These graphical tools allow for visualizing process data over time, displaying the variation in a process and helping to determine whether it is operating within acceptable limits. Common types of control charts include:
- X-bar and R charts for monitoring variables data, such as weight or temperature.
- p-charts and c-charts for attributes data, such as defects per unit or defect rate.
- Process Capability Analysis
Process capability analysis measures a process’s ability to produce outputs within specified limits. Capability indices like Cp, Cpk, and Pp are used to assess whether a process is capable of consistently producing results within acceptable limits. High capability values indicate a stable and predictable process. - Root Cause Analysis (RCA)
When a process shows variation or deviates from the expected outcome, identifying the root cause of the issue is crucial. RCA uses tools like cause-and-effect diagrams (Ishikawa diagrams), the 5 Whys technique, and Pareto analysis to determine the underlying causes of defects or anomalies. - Sampling
SPC relies on periodic sampling to monitor processes without interrupting production. Sampling allows organizations to draw inferences about the entire process based on a subset of data, optimizing resource usage.
By implementing SPC, organizations can identify potential issues before they lead to costly rework, recalls, or customer dissatisfaction. Moreover, SPC supports continuous improvement, a fundamental principle in quality management systems like Lean and Six Sigma.
The Role of Data Analytics in Statistical Process Control
In recent years, data analytics has transformed how organizations approach SPC, providing deeper insights and actionable intelligence. The combination of SPC and data analytics enables companies to go beyond basic monitoring, leveraging data to optimize processes, predict issues, and enhance overall productivity.
Here are some ways data analytics enhances SPC:
1. Predictive Analytics and Machine Learning
Predictive analytics applies statistical models and machine learning algorithms to historical data, identifying patterns that may indicate potential issues. By integrating predictive analytics with SPC, manufacturers can anticipate deviations and address them proactively. Machine learning models can also learn from real-time data, adjusting predictions as new data becomes available, ensuring processes remain under control.
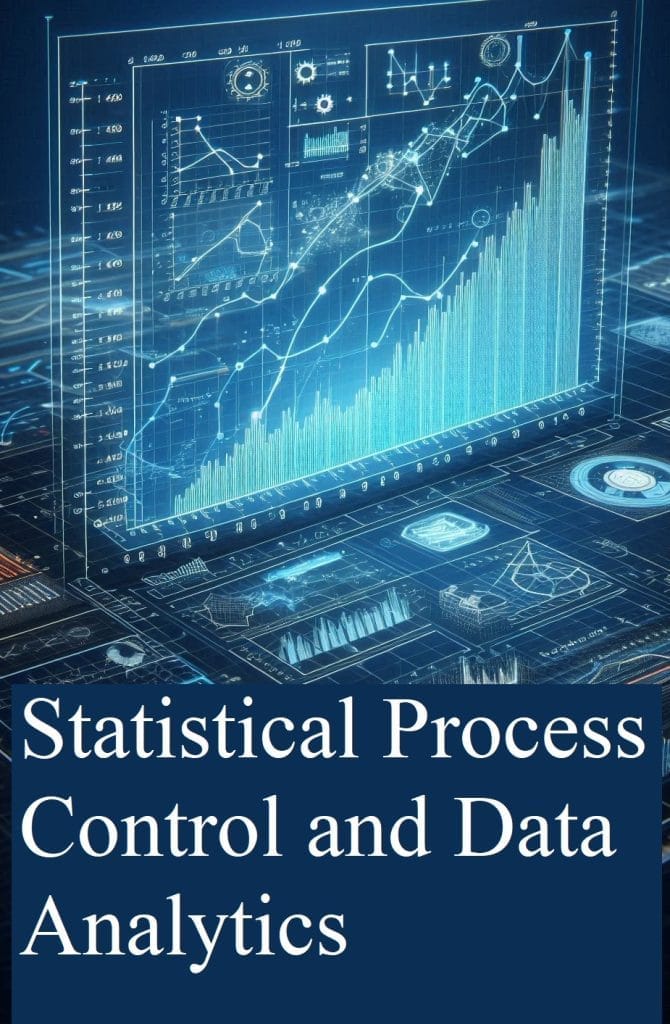
2. Real-time Process Monitoring
Traditional SPC involves periodic sampling, but data analytics facilitates real-time process monitoring. Real-time analytics systems continuously track process variables, allowing for immediate identification of trends, shifts, or outliers. This approach ensures that corrective actions can be taken in real-time, minimizing the impact of process deviations.
3. Big Data and Complex Process Analysis
Modern manufacturing processes are complex, involving multiple variables and interactions. Big data analytics allows companies to analyze vast amounts of data, identifying relationships between variables that may not be apparent through traditional SPC methods. With big data, manufacturers can gain a more comprehensive view of their processes, improving both SPC’s effectiveness and overall product quality.
4. Advanced Control Charting Techniques
Data analytics enables the development of advanced control charts beyond traditional Shewhart charts, such as CUSUM and EWMA charts, which are better suited for detecting small shifts in the process. These charts are particularly beneficial in industries with stringent quality requirements, as they improve the sensitivity of SPC to detect even minor deviations.
5. Automated SPC
Automated SPC systems leverage data analytics to simplify and streamline the SPC process. By automating data collection, charting, and reporting, manufacturers can reduce human error, save time, and focus resources on analysis and corrective actions rather than manual data handling.
Implementing SPC and Data Analytics: Key Considerations
While SPC and data analytics can significantly improve process efficiency and product quality, successful implementation requires careful planning and consideration. Here are some essential steps for integrating SPC and data analytics into manufacturing processes:
1. Define Goals and Objectives
Establish clear objectives for SPC and data analytics initiatives, aligning them with organizational goals such as reducing defects, improving customer satisfaction, or optimizing resource use. Clear goals ensure that resources are focused on meaningful areas and provide metrics for measuring success.
2. Choose the Right Data and Metrics
Select data that accurately represents the process and is relevant to the goals defined. Key metrics might include defect rates, cycle times, process variability, and overall equipment effectiveness (OEE). High-quality data is essential for meaningful analysis, so ensure accurate and reliable data collection.
3. Use the Right Analytical Tools
Choosing the right tools is crucial. SPC software packages are widely available and often include analytics features, but in complex manufacturing environments, custom analytics solutions or integrations with enterprise resource planning (ERP) systems may be necessary.
4. Train Staff and Encourage a Quality Culture
SPC and data analytics require skilled personnel who understand statistical methods, data interpretation, and the specific processes in which they are applied. Regular training ensures that team members are competent in using SPC tools and interpreting data insights. Additionally, fostering a culture of quality encourages employees to take ownership of process improvement.
5. Review and Adapt
SPC and data analytics are not one-time implementations; they require continuous review and adaptation. Regularly evaluate the effectiveness of control charts, the relevance of metrics, and the accuracy of predictive models. Adjustments should be made as processes, products, and customer requirements evolve.
Applications of SPC and Data Analytics Across Industries
While SPC was initially developed for manufacturing, its principles are now applied in various industries, including healthcare, finance, and logistics. Here’s how SPC and data analytics are making an impact beyond manufacturing:
1. Healthcare
SPC is widely used in healthcare to monitor the quality of care and outcomes. For example, hospitals can use SPC to track patient wait times, surgical outcomes, and infection rates, while data analytics can predict patient surges, optimize staff schedules, and identify areas for improvement in care delivery.
2. Finance
In finance, SPC and data analytics are used to detect fraud, monitor transaction processes, and manage operational risk. By analyzing transaction data, financial institutions can identify unusual patterns or anomalies, minimizing the risk of fraud or regulatory compliance issues.
3. Supply Chain and Logistics
Logistics companies use SPC to monitor shipment times, inventory levels, and delivery accuracy. Data analytics enhances this by predicting demand, optimizing route planning, and identifying potential bottlenecks in the supply chain, ultimately improving efficiency and reducing costs.
4. Energy Sector
SPC and data analytics help energy companies optimize production, monitor equipment health, and improve safety. Predictive maintenance, powered by analytics, enables companies to anticipate equipment failures before they occur, avoiding costly downtime and ensuring the consistent supply of energy.
Benefits of Integrating SPC and Data Analytics
The integration of SPC and data analytics offers numerous benefits, from improved quality control to cost savings and better customer satisfaction. Here are some of the main advantages:
- Reduced Process Variation: SPC ensures that processes remain stable, reducing the likelihood of variation and defects. Data analytics further enhances this by identifying trends and patterns that indicate potential issues, enabling proactive intervention.
- Increased Efficiency: By identifying inefficiencies and bottlenecks, SPC and data analytics can improve overall process efficiency. Real-time monitoring and predictive analytics allow organizations to streamline production, reduce waste, and maximize output.
- Enhanced Decision-Making: SPC and data analytics provide data-driven insights that support better decision-making. Rather than relying on intuition, managers can use objective data to optimize processes, allocate resources, and prioritize improvements.
- Cost Savings: By minimizing waste, defects, and rework, SPC and data analytics help reduce costs. Predictive maintenance, for example, allows organizations to avoid costly repairs and downtime, while process optimization minimizes material and labor costs.
- Improved Customer Satisfaction: Consistent quality and reliable delivery build customer trust and satisfaction. By using SPC and data analytics, companies can consistently meet or exceed customer expectations, creating a competitive advantage.
Challenges in Implementing SPC and Data Analytics
Despite the benefits, organizations may face challenges when implementing SPC and data analytics, including:
- Data Quality and Integration: For accurate analysis, data must be clean, consistent, and integrated across various systems. Poor data quality can lead to incorrect conclusions and ineffective interventions.
- Cost of Implementation: Implementing SPC and data analytics can require significant investment in software, equipment, and training. However, these costs are often offset by the resulting improvements in efficiency and quality.
- Resistance to Change: Employees may resist changes to established processes. Change management and training programs are essential to ensure team buy-in and effective use of SPC tools.
Conclusion
Statistical Process Control and data analytics are essential tools in the modern industrial landscape. Together, they provide a powerful means to achieve process stability, optimize production, and enhance quality, enabling companies to meet stringent standards while reducing costs. When implemented effectively, SPC and data analytics not only improve process efficiency and product quality but also provide a competitive edge in an increasingly demanding market.